top of page

Tower fan project inspired by the complex yet straightforward structure derives from the essential architectural elements. The project looks at the classic down rod design of the fan, and by using the trellis elements as the downrod design creates an entirely new way to suspend the fan from the ceiling. The structure uses the simple one-piece mould in housing complemented by the minimal blade design that genuinely brings this fan's essence and focal point.
Tower fan is the reinterpretation of modern architecture within the classical fan design
Clients
Cyan Design
Status & Date
Completed 2024
Project Types
Ceiling Fan Design
Zephyr
2024
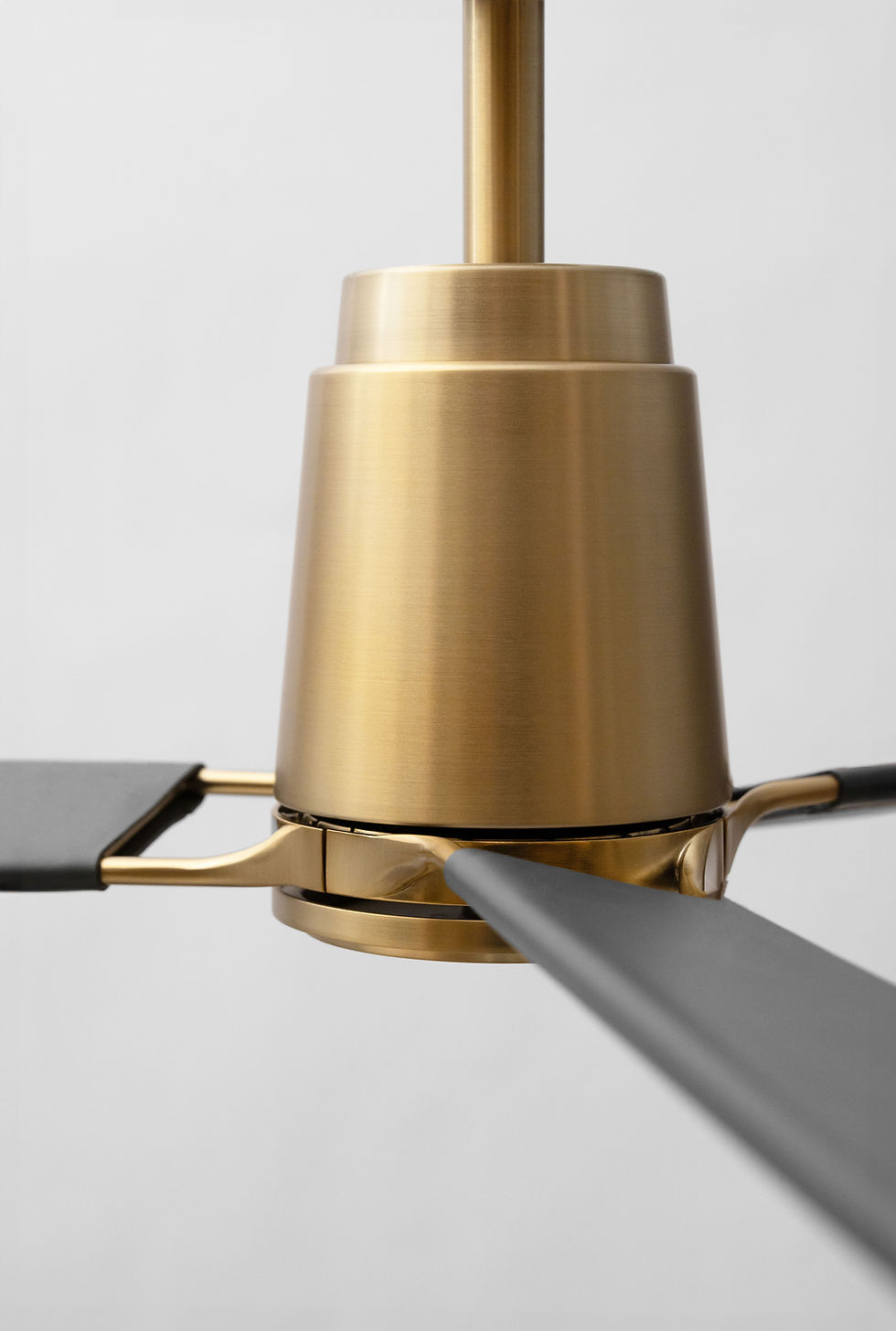

1. Tower fan, Elevation view / © Studio Kubrick
2. Tower fan, Bottom view / © Studio Kubrick





1. Tower fan, Elevation view / © Studio Kubrick
2. Tower fan, Bottom view / © Studio Kubrick
2. Tower fan, Bottom view / © Studio Kubrick

1. Raw metal materials / © Studio Kubrick
2. Selections of tooling, metal workshop / © Studio Kubrick
3. Sanding process, canopy component / © Studio Kubrick

The depth of the metal embodies structure and emphasises form through manufacturing
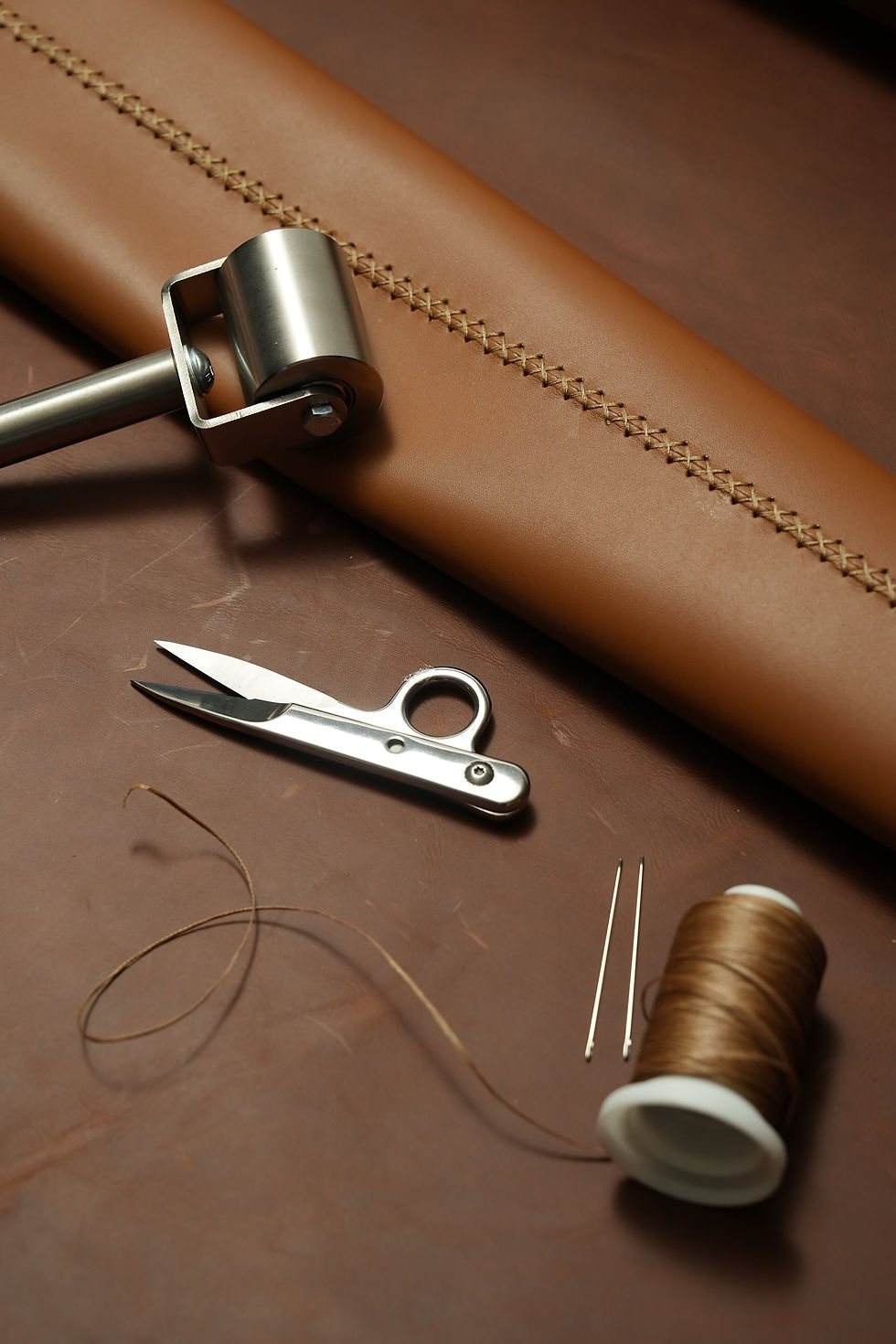
The intricate details make it challenging during the manufacturing process, as the delicate structure of the suspension needs to be welded by hand. As a result, we have combined two different methods of the fabrication process with both welding for the trellis structure and the die-cast metal to form a bottom motor housing and canopy. First, the die-cast is formed by pouring molten metal into a reusable mould – and the structure is deep drawn: a process that involves forcing cold metal through a die to shape it.

The depth of the metal embodies structure and emphasises form through manufacturing
The intricate details make it challenging during the manufacturing process, as the delicate structure of the suspension needs to be welded by hand. As a result, we have combined two different methods of the fabrication process with both welding for the trellis structure and the die-cast metal to form a bottom motor housing and canopy. First, the die-cast is formed by pouring molten metal into a reusable mould – and the structure is deep drawn: a process that involves forcing cold metal through a die to shape it.

bottom of page